

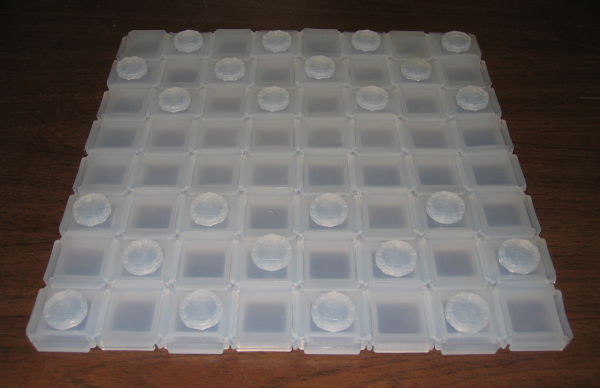
Problems, frustrations, difficulties, and solutions:
When generating tool paths we encountered areas that were too small for the tool due to adding draft to the part. Luckily Unigraphics makes it easy to make small adjustments to sketch measurements that then cascade changes down to the final part, making it not as much of a problem. It was still annoying, and in the future more care needs to be taken in remembering draft in all measurements.
When an entire class needs to prototype within a week, a matter of hours can make the difference in having your final parts days or hours before the final presentation. Yet another lesson in punctuality.
On the checkerboard, if each hook were slightly shorter, the parts may become easier to fit together. Also, for some reason the top corner filling block didn't get fully machined out, and would be easy to fix next time.
We had hopped the machine tool paths left on the top surface of the checkerboard pieces would more clearly distinguish which tiles were flipped 90°. if different colored plastics still arn't available, gooves could be cut on the top surface to clearly define each tile.
If possible, a larger mold could fit more parts at once, thus greatly decreasing the production time. If not, perhaps miniaturization would be an option worth investigating.
Looking at the checkerboard also screams out 'disco floor' to me, and it could be fun to place little colored diodes and watch batteries in the cavities beneath each tile. This may then open the door to even more innovations in game play.
